Galvanized steel (which is protected by a coating of zinc metal) is found everywhere and all around us, used to make stimulating products. The steel’s resistance to breaking is strengthened and enhanced by the metal. Despite its diverse applications, the primary advantage of galvanized steel is its resistance to corrosion. This advantage makes it an integral part of many industries like automotive, construction, aircraft, and even road safety equipment, specifically crowd control barriers and temporary fence panels. In this article, we will cover galvanized steel strength along with its practical uses, appealing qualities, and applications.
What Is Galvanized Steel?
Galvanizing is the process of covering iron with a layer of metal to protect it and prevent rusting. Although there are various methods, hot-dip galvanizing is the most popular type of method. Because it combines the strength and shape of steel with a protective coating that helps prevent rust, galvanized steel is a highly sought type of steel. By serving as a barrier against harm from other compounds, zinc aids in protecting a collection of chemical elements. This specific kind of coating offers superior support and is long-lasting. That is the reason steel is given an outer layer of metal to make it stronger and more rust-resistant. ASTM A653, EN 10346, and JIS G3302 are among the standards that regulate the coating’s machine-like qualities and thickness.
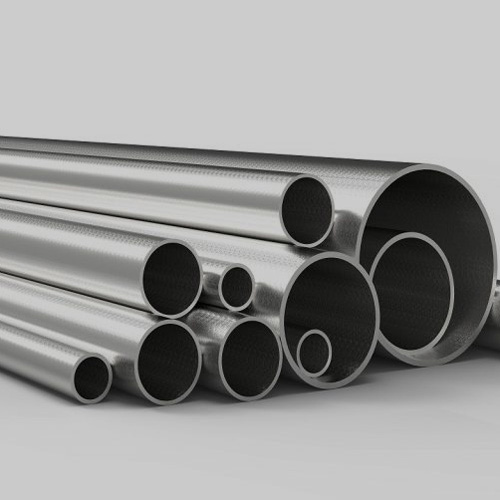
How Does the Galvanizing Steel Process Work?
Manufacturing process of galvanized steel is very simple. Surface preparation, zinc immersion, and finishing treatment are the three primary steps in the galvanization process. The steel is first thoroughly cleaned using a particular solution, and then it is treated with hydrochloric acid.
The manufacturing process of galvanized steel is easy to understand. The producer frequently submerges steel in molten zinc, which is heated to about 450 degrees Celsius. Like any other mixture, the zinc adheres to the steel and creates a connection between the iron and zinc. Zinc’s incorporation with steel gives it the characteristics of both metals. Hot-dipping is the most commonly used method of galvanization. Zinc can be sprayed on steel, although the layer will be thinner. The galvanized steel coating shields the underlying metal from the elements and aids in preventing rusting. Finally, chemical treatments are applied to the steel to improve its protective coating. A consistent zinc coating with a thickness ranging from 0.5 to 39 mils is guaranteed by this procedure.
Different Types of Steel Galvanization
Galvanized steel can be categorized into five major types, each of which has an impact on the kind of coating that is created and the potential use for the steel. The five types that are mentioned are as follows:
Type 1. Galvannealing
Hot-dip galvanizing and annealing (heat treatment) are combined to create the distinctive coating that galvanizing produces on steel sheets. The wrapped object may be made of iron and zinc, and paint will stick to its dark, matte surface perfectly. The metal is first dipped in hot zinc and then baked at roughly 565 °C to make the interaction between the steel and the liquid zinc easier.
Characteristics
- It provides exceptional protection outside and during extreme weather conditions due to its thick zinc coating, which also makes it resistant to erosion.
- The bond between zinc and steel strengthens the coating’s resilience to wear and tear.
- By ensuring complete coverage, even in corners and along edges, uniform coating helps to minimize weak areas.
- When little dings or scratches happen, zinc helps protect exposed steel
- By protecting exposed steel from tiny scratches or damage, zinc helps the steel mend itself. Over time, prices are reduced because it requires little maintenance.
Frequent Uses: Galvannealing is used for resistance welding, marine applications, and any other application requiring extreme stretching.
Type 2. Hot-Dip Galvanizing
Hot-dip galvanizing is a zinc coating method for steel sheets or other steel products. This happens when steel items are cooled after being sprayed with liquid zinc. Inside the steel, the zinc adheres to the press. Hot-dip galvanizing stops the metal from rusting by creating a coating on both sides of it. Galvanized steel does not need any further paint or treatment.
Characteristics
- Provides a consistent surface that is perfect for painting and decorative applications.
- Offers precise control over thickness for improved performance and reduced weight.
- Best suited for interior applications or low-corrosion settings.
- Makes molding, stamping, and shaping formidable.
- Welding is made easier by thin coatings.
Frequent Uses: Hot-dip galvanized products include supports, fasteners, highway guardrails, and durable brackets, fixings, and flooring.
Type 3. Electrogalvanizing
The electrogalvanizing process applies a zinc layer to steel using electricity. A zinc coating is applied to steel by immersing it in a zinc solution using a specific electric current. A thin film of zinc is left behind when the current interacts with the steel surface and the zinc salt. The zinc coating produced by the hot dipping method is thinner.
Characteristics
- Provides a smooth painting surface without the need for extra prep work.
- The steel’s lifespan is increased by the special coating’s strong adhesion.
- Still appropriate for a variety of applications, although a little less safe than pure zinc coatings. Compared to pure zinc, the zinc-iron combination is much more resilient to scratches.
Frequent Uses: Electrogalvanized steel finds use in ceiling tiles, door frames, and control panels.
Type 4. Pre-Galvanizing
Pre-galvanizing, sometimes referred to as mill galvanization, is the first stage of producing metal goods that will not undergo substantial subsequent formation. Rusting is more likely when working with galvanized steel since any kind of handling exposes the metal to air. The most popular types of pre-galvanized components are steel sheets and rods.
Compared to traditional hot-dipping, this method allows for faster and more efficient galvanizing on a larger scale. To prepare it for dipping into liquid zinc, the sheet metal (or other formed steel) is rolled through a cleaning machine. The zinc is then promptly removed. Pre-galvanized materials are frequently those that have a particular shape before they are cut.
Characteristics
- Superior productivity maintains high quality while reducing waste.
- Constant training allows for substantial output with little waste. Surface matte is perfect for jobs like painting or molding since it is clean and smooth.
- It provides outstanding defense in a range of situations, especially in mild to moderate climates.
Type 5. Thermal Diffusion Galvanizing or Sherardized Steel
Sherardized steel or thermal diffusion galvanizing is a type of galvanized steel that has undergone a dry zinc coating process. This creates a consistent layer of iron and zinc. It conforms with ISO 17668 and is commonly used for small goods like fittings and clips. Handle of Sherardized Steel
In the sherardizing process, steel parts are heated to temperatures between 300 and 450 degrees Celsius (572 and 842 degrees Fahrenheit) in a drum containing zinc powder. Iron and zinc combine to form a solid when zinc diffuses and evaporates onto the steel surface. This method works particularly well for small, complex pieces. Sherardized steel characteristics include:
Characteristics
- Offers even and a consistent layer, even on tiny parts and odd forms.
- Functions effectively in challenging conditions, including water and situations involving heavy use.
- Compared to pure zinc, the combined coating is more resilient and long-lasting.
- Since the dry process produces no liquid waste, it is environmentally beneficial.
Advantages of Galvanized Steel
1. Corrosion Resistance
Between the steel and material components like air and fluids, a thin layer of zinc metal serves as a physical barrier, concealing the galvanized steel underneath. Despite the covering being scraped, rust does not spread rapidly or significantly. Coastal domains, industrial zones, and high-humidity areas are some of the harsh environments where hot-dip galvanized steel is best suited.
2. Longer Lifespan
By promoting its special resistance to disintegration, steel may endure more deterioration for decades. In typical rustic settings, it can live for up to 50 years. In more hostile environments, like modern or coastal settings, it usually only loses 20 to 30 years of its basic wholeness. Because of its durability, it’s a great alternative to completed structures like bridges, houses, and infrastructure.
3. Low Maintenance
Steel rarely requires repair, replacement, or maintenance because it resists rust and weather deterioration so well. In the long run, this reduces the cost of materials, labor, and occasion for the product. Galvanized steel, whether used for support structures, cover, or rustic fencing, does not need routine upkeep.
4. Cost-Effective
Fourth. While the initial cost of galvanized steel may be slightly higher than that of non-coated options, the long-term financial benefits of this investment are substantial. Additionally, because galvanizing is a process that usually only needs to be completed once and does not need to be repeated, unlike paint or powder coating, it helps save ongoing costs. It is therefore a reasonable approximation of the product’s lifespan.
5. Quick Inspection
One of the main benefits of galvanized steel is how easy it is to check its condition. Most of the time, you can determine if the coating is broken or pressed in just by looking at it; complex testing or equipment is not necessary. Reviewers, development directors, and support personnel can now quickly evaluate more health without having to pay testing fees.
What Industries Utilize Galvanized Steel?
Solar & Wind Sector
Once they get going, businesses that focus on the wind and sun have to keep going. If maintenance or repairs are required, it could interfere with their income. This suggests that the hot-dipped galvanized steel’s ability to prevent corrosion is well recognized in solar energy applications. It is also renowned for being environmentally beneficial because it produces no emissions and may operate for many years without maintenance. For example, farm machinery is widely used in agriculture since it is prone to wear and tear. More durable equipment is therefore needed, even in challenging agricultural environments. Hot-dip galvanized steel offers long-lasting rust prevention that can last for many years.
Construction Industry
For more than a century, galvanized steel has been a common material in the construction industry for both residential and commercial applications due to its strength. It is also chosen for construction due to its attractive appearance. Galvanized steel is frequently used in modern buildings and has a glossy surface that gives it a modern appearance. Additionally, compared to minor components like railroads, pipelines, parking bollards, road barriers, ditches, and more, it is used disproportionately for larger components.
Road Safety Barrier Sector
Galvanized steel is the perfect material for crowd control barriers since it is extremely durable and resistant to the harsh outdoor environment. These roadblocks are commonly used in construction sites, sporting events, concerts, parties, traffic safety programs, and other locations where large crowds need to be controlled or kept under control for safety and order. They are essential in maintaining pedestrian safety and stopping unauthorized access to areas that are off-limits.
But why is galvanized steel tube used in these fences? Galvanized steel’s exceptional resistance to rust is one of the main reasons it is utilized in these crowd control barriers. Equipment is subjected to rain, humidity, grime, and in some cases, salt, during outdoor events and roadside use. Even after prolonged exposure to moisture, the zinc coating on galvanized steel serves as a barrier to keep rust from developing. This suggests that the crowd control barriers can be deployed frequently and utilized for extended periods of time without needing regular maintenance or repainting. But not all galvanized steel crowd control barrier suppliers give you the same products. We are proud to offer road safety and traffic safety equipment according to your project specifications and budget.
Why Galvanized Steel Is Ideal for Road Safety Equipment:
For outdoor applications where the material may be subjected to precipitation, snow, or sunlight, weather resistance is essential.
- The weather resistance of galvanized steel makes it a great material for road safety devices.
- Able to withstand rough use, accidental collisions, and vandalism.
- Ideal for event planners who wish to avoid the hassle of regular upkeep.
- It keeps a consistent and expert appearance across several products.
Galvanized Steel Vs Stainless Steel
Both stainless steel and galvanized steel are rust-resistant, however they are utilized for various reasons and have different rust-resistant mechanisms. Galvanized Steel tube used for crowd control barrier/steel barrier has been coated with zinc, which is known as galvanized steel. This zinc covering protects the steel against rust and environmental damage. It is a well-liked option for outdoor, agricultural, and construction applications due to its affordability, simplicity of use, and resilience in challenging conditions. However, if the zinc covering erodes or is damaged, the steel underneath may start to rust.
Stainless steel is enhanced with chromium to help create a self-healing protective coating. This offers it a great resilience to wear and tear, even in extreme settings like those found aboard ships or exposed to chemicals. Despite being more expensive than galvanized steel, it is of higher quality, lasts longer, and looks better. Stainless steel is a top choice for high-quality tools, medical equipment, food processing machines, and companies where rust resistance, cleanliness, or aesthetics are important considerations.
Conclusion
Today, galvanized steel is the primary material used by many businesses. The galvanization process is carried out by well-equipped companies that have the tools required to produce coated steel that satisfies safety standards and can satisfy the particular needs of each project. Being a traffic safety manufacturer, we are ready to meet all of your galvanized steel requirements with superior dependability and quality as compared to market standards. JACKWIN is dedicated to excellence and ensures, as a road safety supplier in China, that all of its manufactured road safety equipment meets stringent standards. Our galvanized steel manufactured crowd control barriers provide reliable and effective solutions for road development, automotive, machines, and other safety related projects. If you wish to move on with your road safety project using galvanized steel, you can get in touch with us right now to talk with our experts and get a quote.