Plastic fabrication is what you use when you need to shape, cut, or create flexible materials into useful pieces in large quantities. Whether you’re working on original designs, signs, landscaping, or machine parts, knowing the right strategies can help you choose the best way to proceed with your project. This guide takes you through the basics of plastic fabrication.
What’s Plastic Fabrication?
Plastic fabrication is a process whereby plastic is processed into a desired shape according to the project’s requirements. To turn an inexperienced or raw plastic material into a beneficial and custom shape, plastic manufacturers treat it correctly via the plastic fabricating process, but the method of processing varies depending on the type of material. Plastic production is the fabrication process of forming plastic sheets or blocks into specific shapes.
For example, we observe and visualize plastic parts and plastic components, from home machines to buses and machining tools, in our daily lives. Plastics are lightweight and inexpensive; they are excellent for creating different types of products and can be used to make prototypes and for large production results. For instance, the vacuum casting process heats up the plastic to shape it, while CNC machining cuts or removes the material using rotating techniques and tools.
Different Types of Plastic Fabrication Processes
1. Cutting Method
You request exact shapes and clean edges since sharp cutting is one of the smoothest and most practical designs. You will be in charge of complex product designs like saws, routers, laser cutters, or CNC machines, regardless of how advanced your products are. It works well for covering simple and intricate plastic objects.
2. Plastic Welding Process Method
Welding allows two manufactured components to be joined by applying heat to their contact surfaces. You can employ methods like rapid ultrasonic welding or hot gas welding, depending on the requirements and kind of material. This method is fantastic for establishing solid, sensible connections in pipe systems, tanks, and conduits.
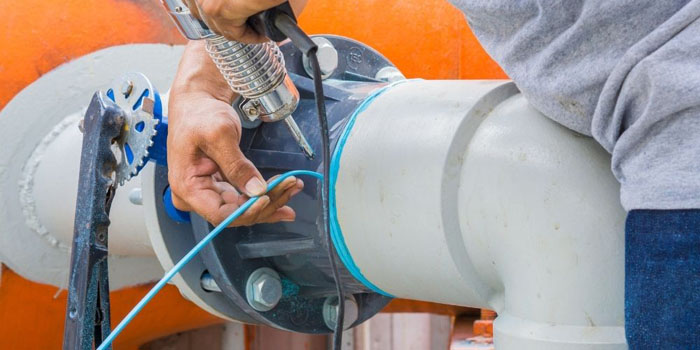
3. Blow Molding
Whether you are making purge things like holders or containers, blow molding is the way to go. You fill a warm, delicate plastic with the required shape it gets to be a shape. This blow molding hand process makes it simple to quickly produce special, straightforward, and solid custom plastic parts. In plastic blow molding, you can get three diverse options.
- Extrusion blow molding
- Injection blow molding
- Stretch blow molding
3. Plastic Extrusion
In plastic extrusion, you smooth and thrust the fabric through an uncommon opening to form long, level pieces like tubes or sheets. It’s a unique plan on the off chance that you would like a part of uniform shapes for larger units. You’ll discover it to be persuasive and cost-effective for numerous machine-like uses.
4. Rotational Molding
Once you utilize the turning process, you put adaptable powder into a shape and then turn it while warming. The adaptable fabric breaks down and covers the interior of the form, making expansive purge spaces. You will discover it incredible for making things like huge tanks or spaces behind house slides.
5. Vacuum Casting
When there’s nothing interior, you pour a liquid into a silicone mold that helps it move effortlessly with vacuum pressure. This method evacuates bubbles and gives a smooth, decent finish. You’ll find how to make high-quality sample models or small production runs with extraordinary outcomes.
5. Forming (Thermoforming/Vacuum Forming) Method
If all you want to do is form plastic into a mold frame, forming is the best technique. Thermoforming is the technique of heating a plastic sheet to its maximum temperature and then shaping it over a frame mold with pressure or vacuum. Package bundles, plates, sheets, and lodge housing can all be made effectively using this technique.
6. Machining Process Method
Using instruments like drills, mills, and machines, machining is the process of forming plastic into incredibly accurate pieces. It will be profitable while working with thicker materials or when you require near-resilience and tight tolerance. It is extensively utilized in aviation equipment, medical equipment, and specialized industrial equipment.
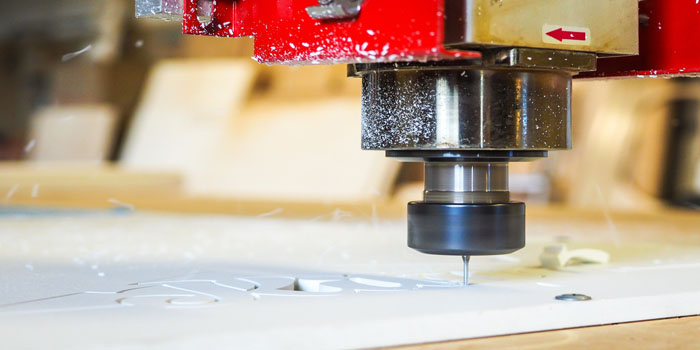
7. Bonding (Adhesive Joining) Method Process
When interface welding is not an option, fabricated pieces are joined using bonding adhesives. You should select the right glue based on the kind of plastic and the intended result. It is a tidy, simple way to collect signs, looks, and intricate components.
8. Injection Molding Process
For high-quality large production, no doubt that injection molding is profoundly able. You implant fluid plastic into a shape, permit it to cool, and pop out the wrapped-up portion. It is broadly applied in client items, fittings, and limousine businesses.
9. 3D Printing (Additive Manufacturing)
Going with 3D distribution, you will be able to construct plastic fabricated parts layer by layer, turning to digital design. It is especially useful when you are prototyping or changing complex geometries. You will consider this method perfect for charm speed, flexibility, and inconsequential material misuse.
10. Thermoforming
Thermoforming is a process where plastic coating is warmed just some time before we shape and bend it, at that heating point it is shaped over a required shape with pressure or vacuum. It is took advantage of for bundling, car parts, and pointless mugs.
11. Plastic Pultrusion
Pultrusion gives consent to be a tireless process in progress manufacturing of composite materials with normal drawing of individual parts of the component. It incorporates drawing in discourteous materials through a warmed pass on to create things like bars, pillars, and leggings.
12. Die-Casting
This die-casting handle may be straightforward and easy to model. First, the manufacturer will create a unique die form to use as a demonstration. This unusual pass-on tool will allow you to later cut flexible sheets into the desired pieces. In general, the die casting could be a quick and inexpensive process. It has a high place in the mechanical, electronic, and communication divisions. Styrene, vinyl, ABS, polyethylene, polypropylene, and other plastic compounds appear to be included in this common type of plastic.
Purposes & Advantages of Plastic Fabrication
1. Parts Customization
You may customize plastic textures to take on unusual shapes, sizes, and forms by using plastic creation. It allows you to fulfill certain shapes and favorable circumstances, whether you are making final products or prototype models.
2. Production Output
Plastic speeds product generation through the use of several production procedures, including as plastic for molding, welding, shaping, assembling, and forming. It is particularly useful for accurately manufacturing intricate pieces, reducing plastic fabric waste, and expediting the production process.
3. Economic Plastic Manufacturing
Creation shapes are useful and versatile, and plastic is frequently less expensive than glass or stone. For exchanges wishing to transmit assets in undamaged condition, this makes it an affordable option.
4. Flexibility Across Industries
Plastic manufacturing has a wide range of uses, from photoelectric cells to useful medical equipment and pickup parts. It accommodates elaborate and sophisticated items in addition to lightweight ones.
5. Performance and Quality
Parts made of plastic are extremely resilient to weather, chemicals, and environmental conditions. This guarantees long-term performance, especially in areas where items made of other materials could fall.
6. Product Development and Prototyping
Fast prototyping is made possible by fabricated plastic, which enables you to test and refine designs rapidly. This makes things better and more unique, which speeds up the market approach.
How to Choose the Right Plastic Fabrication Process
1. Examine the Application
Start with the specific purpose for which the manufactured plastic will be used. Will it be subjected to pressure, weight, chemical substances, or heat? Your selection of surface and handle will be coordinated by the execution conditions of your use.
2. Determine Compatibility of Structure
Not every kind of plastic responds well to every process of manufacture. Many plastic varieties, for example, are more suited for welding, even though the rest of the material actually adheres better to adhesive. The activity you choose fits the properties of your material, such as its thickness, melting point, and unbending nature, in accordance with the requirements of your project.
3. Consider Quantity
Are you carrying thousands of units in bulk, or are you doing a one-time demonstration? In reality, injection molding is best for large production runs due to its exaggeratedly high starting cost but short-run cost per unit, whereas 3D printing or machining allow for more cost-effective operation for short-run capacities.
4. Complexity of Design
Important but basic shapes can be managed, such as when cutting or forming is needed, but intricate patterns with precise tolerances need to be machined, delivered, or 3D printed. When selecting the right frame, your design gauge, central focuses, and dimensional accuracy are important considerations.
5. Financial Restrictions
More costly but more lucrative tools or equipment are needed for any shapes that need CNC machining and injection molding. Think about your budget for both processes because some have gotten more authentic while still providing long-term and cost-effective solutions.
6. Time and Speed
How soon would you like your parts to arrive? Sharp results may be transmitted via shapes like 3D printing and laser cutting, which makes them perfect for short turnaround times or rapid prototyping.
7. Final Finish Beauty
You will need an efficient technique that transfers clean edges and smooth wraps up for important results, including appearances, area limitations, or consumer items.
What Are the Uses and Examples of Fabricated Plastic Products?
There are many advantageous of plastic produced parts because of its sturdiness, versatility, and cost-effectiveness, fabricated plastic parts are used in many different industries. To create customized parts that are safe in terms of range, appearance, and can withstand chemical compounds, humidity, or adverse effects, you will have to rely on them.
1. Automotive Industry
You use manufactured plastic for small sheets and covers, and you observe internal components to reduce vessel weight and improve fuel economy.
Examples: Under-the-hood covers, battery secure locations, and instrument board trims.
2. Medical Industry:
Because plastics are clean and non-sensitive, they are advantageous in medical jobs.
Examples: surgical equipment cases, defensive observers, restorative plates, and device accommodations.
3. Electronics Industry:
These companies create dimensional accommodations for gadgets and develop plastic shapes that are unique.
Examples include PCB component boards, rope organizers, switch secure regions, and semiconductor coverings.
4. Retail and Display:
You can employ flexible display creation to create unique, visually striking looks that are weather-resistant.
Examples include object stands, brief holders, and point-of-sale displays.
5. Construction Industry:
Because of its resistance to disintegration and UV permeability, you use manufactured plastic in the construction department.
Examples include Wall cladding schematics, pipe fittings, sky and structural wrap-up window covers, and outside wrap-ups of dividers.
6. Food & Beverage Industry:
Fabricated plastic provides hygienic, sanitary, easy-to-clean methods for handling and preparing nourishment.
Cases: Capsule coverings, feeding plates, and sharp sheets.
7. Agriculture Industry:
You agree to accept plastic delivery for robust, weather-proof solutions in agricultural developments.
Examples include preschool sheets, creature-equip observer sheets, and accessible water sheets.
8. Aerospace Industry:
You employ parts that are created to be both powerful and inconspicuous in order to adapt to high-depiction situations while in flight.
Cases: ductwork parts, specialized casings, and cabin sheets.
Which Plastic Material Does Plastic Fabrication Use
Here is the answer to a common question that arises in our minds: What plastic is made from?
Acrylic (PMMA)
Acrylic plastic is used in flexible designs because of its lightweight nature, UV resistance, and clear look. Acrylic and plastic are frequently used for signs, glasses cases, and locations that require mirrors.
Polycarbonate (PC)
Polycarbonate (PC) is renowned for its strength and exceptional resistance to impact. If you need tools, watches, shields, or basic panels, it is advisable to get them first.
Polyethylene (PE)
Strong and pliable, polyethylene (PE) is a material that resists moisture and chemicals well. It can be applied to liners, cutting sheets, and owners in both agricultural and industrial settings.
Polypropylene (PP)
Polypropylene (PP) is excellent for food containers, maintenance items, and automobile parts where strength is crucial because it is extremely robust and does not react with chemicals.
Polyvinyl Chloride (PVC)
PVC, or polyvinyl chloride, is a robust substance that adheres well and does not degrade. Because of this, it can be used for pipelines, electrical insulation, and other objects in both indoor and outdoor environments.
Acrylonitrile Butadiene Styrene (ABS)
Strong and pliable, Acrylonitrile Butadiene Styrene (ABS) is a material that is simple to mold and shape. It is frequently found in models, automobile parts, and solar panels.
Nylon (Polyamide)
Gears, bushings, and moving machine parts are frequently made of nylon (sometimes called polyamide) because of its strength, durability, and ability to withstand heat.
High Impact Polystyrene (HIPS)
The new trend, polystyrene, is smooth and easy to form for printing. You handle it primarily for temporary packaging designs, trade shows, and signs.
Polystyrene (PE)
Polystyrene is a difficult plastic frequently used for disposable forks, food containers, and CD cases. It can be clear or vague and is simple to create and alter. The truth is that it’s cheap, but PS is delicate and doesn’t handle heat exceptionally well. Long polystyrene (co-recorded materials) is frequently utilized in packaging and insulation, which might be a key component.
PET (Polyethylene Terephthalate)
PET (Polyethylene Terephthalate) could be a solid and adaptable plastic that’s frequently utilized for beverage holders, food bottles, and materials like polyester. It’s known for its appealing plan, incredible feel, and capacity to be reused. PET is light, solid against hits, and secure for nourishment, making it incredible for bundling.
POM (Polyoxymethylene)
Acetal, also referred to as POM (Polyoxymethylene), is a strong, low-friction-fighting plastic that is widely used in precision items like gears and automobiles. For strength, you will value its toughness, which relates to space strength, and resistance to wear and tear.
JACKWIN – Your Custom Plastic Road Safety Manufacturer
Customized plastic road safety products’ manufacturing according to personal requests is part of our plastic fabricators’ expertise. For example, either utilizing specific lying procedures for vehicle parts, making particular designs for road safety items, or selecting the suitable surfaces for road barrier modules, we cover you all.
So, for a plastic fabrication company or any government-led road projects that require these specific things, our custom plastic services are vital. For tough, well-organized street security items, Jackwin is your trusted accomplice & plastic manufacturing company. Our specialization is custom plastic road safety and street security products. We offer delineators, barriers, high-depiction custom cones, and signs. Being a traffic safety products supplier and tap plastics supplier, we guarantee our items are designed to follow security standards and endure tough environments in extreme situations.
Jackwin is committed to quality and customization, making beyond any doubt your company get the reliable, long-lasting, custom manufacturing they require. Require advanced data? Get in touch with us and clarify your questions thoroughly!
Conclusion
Plastic manufacturing makes modern openings, whether you’re changing devices or making huge mechanical parts. By learning about the diverse strategies, textures, and finishes, you’ll be able to make superior choices that lead to more effective, long-lasting, and cost-saving outcomes. Utilize the fabrication of plastic to assist you in making your plans and concepts come to life.
Plastic Fabrication Related FAQs
What distinguishes plastic fabrication from plastic extrusion?
Plastic fabrication blend includes making and putting together adaptable sheets or parts by bending, twisting, official, or holding them together. Within the process of alteration, plastic fabric is pushed through a formed opening to form long pieces, like tubes or sheets.
Are fabricated plastic products long-lasting?
Yes, fabricated plastic-related things are by and large solid, particularly when made from solid materials like colored plastic, polycarbonate, or HDPE
What is the function of a mold in plastic manufacturing?
The function of mold is to shape, giving a fluid or delicate fabric a particular shape as it cools and becomes strong. It’s critical to combine activities like pouring and freezing to guarantee exact estimations and smooth surfaces.
What is the difference between blow molding and injection molding?
Blow molding is utilized to make hollow, adaptable things like bottles by heating the material and extending it into a shape. Injection molding includes putting a fluid material into a molded shape to make solid parts with exact points of interest, such as gears or covers.
How do I know the materials to use for my products?
You ought to consider the product’s vital highlights, how versatile it should be, its reaction to temperature, its chemical resistance, and the cost. After you audit different plastics texture datasheets, you can make a stronger, improved, and much better choice for your particular needs.